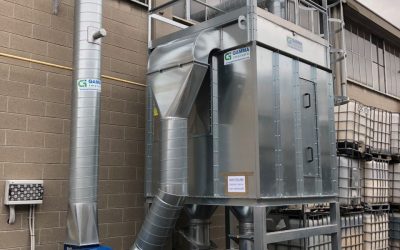
Metal grinding and polishing powder extraction system
Customer request
Extraction of welding fumes and polishing powders produced during metal workings, by capturing them as close as possible to the polluting source as required by the law.
Problem
The customer asks for a powder extraction system capable to grant flexibility of work, taking into consideration that welding and grinding stations sometimes work at 30% of their potential. Hence, it is needed a system working in efficiency in a range of capacity from 29000 mc/h down to the decrease wanted, with no electrical power waste.
Technically, the challenge consists in aspire correctly powders from polishing stations, which scatter micropowders quickly and not easy to catch with classical systems as suction arms and hoods.
Solution
A customized pinpoint extraction system with fumes and polishing powders capture on each working station has been designed and installed through suctions walls with side and upper containments to optimize their capacity.
Welding fumes problem has been solved with articulated suction arms diam.160mm equipped with arm extenders to enlarge the working area.
All extraction stations are connected through a network of galvanized circular section steel pipe, which also reaches a cartridge filter with centrifugal fan with simple inlet located outside the production building. An electrical panel in compliance with Industry 4.0, with inverter and pressure reading, controls actual extraction capacity within pipes, so to control also power employed by the fan and reach maximum energy saving.
Design and development
A customized design of an extraction system like this involves an analysis of plant’s productive needs and layout. Afterwards, our Technical Department develops the project, in this case it consists in:
- Air flow speed measurement, both during extraction and pipe-crossing.
- Calculation of the total pressure losses depending on the filter piping path used.
- Selection of suction walls, benches and arms, so to facilitate operators during their job and, at the same time, capture fumes and powder as close as possible to their source.
- Design and production of special fixtures customized on the plant setting.
- Filter and fan sizing, taking into account the total capacity of the plant and pressure drop of systems connected to it.
- 4.0 electrical panel designed to control the entire system, including automized fan-speed managent with inverter. This modifies in real-time capacity according to how many stations are actually working. All this to reach maximum energy saving.
System in compliance with Industry 4.0
A powder extraction system, to be in compliance with Industry 4.0, must be controlled by computerized systems or managed via sensors and drives. In this specific case, the following features has been implemented, allowing the customer to deduct 50% of the total cost.
- automized fan-speed control with inverter, so to reduce current consuption when needed.
- control on filter clogging level through real-time warning via e-mail, sent to the maintenance service.
- remote and optimized integrated systems management, with anomaly warning.
- anomaly and threshold levels control and warning of each sensors of the system, like rotary air locks, discharge screw or fire sensors.
Extraction systems reference standard
D.lgs. n. 81 from 2008 “Protection of health and safety at the workplace” subsitute of previous D.P.R. n. 303/56 “general hygiene rules for work”, D.P.R. n. 547/55 “Rules for prevention of accidents at work” and DL n. 626/94 “Implementation of the EEC Directives on the improvement of the safety and health of workers”.
sectors of application
MetalworkAssociate systems
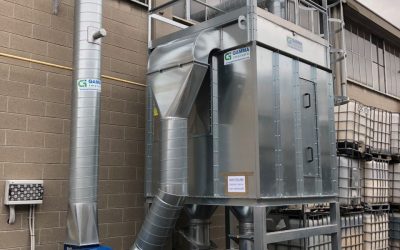
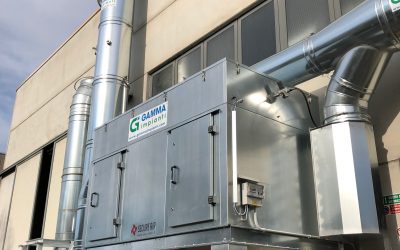
4.0 extraction systems
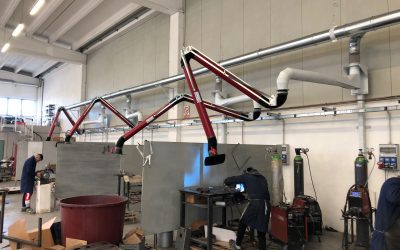
Welding fumes extraction
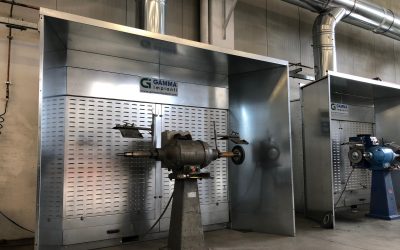
Aspiration for grinding
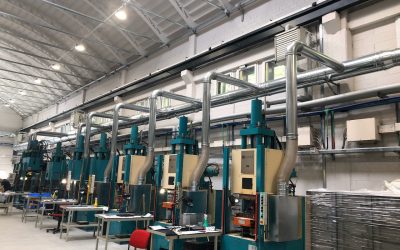
Extraction on the machine
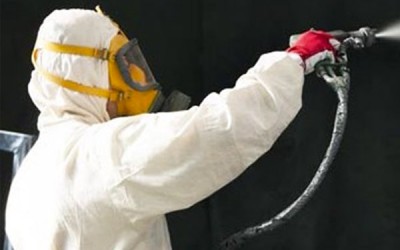
Extraction for varnishing
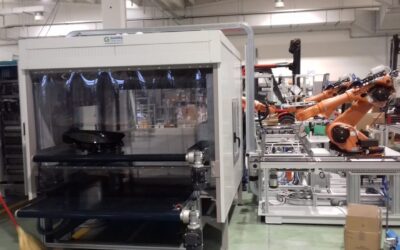
Chip extraction

Noise treatment
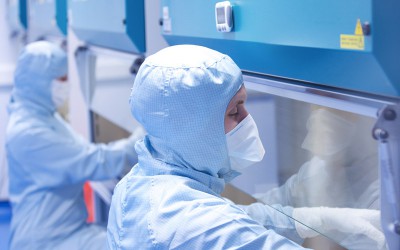
Clean rooms
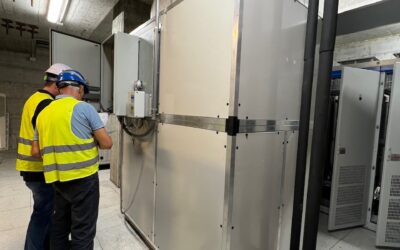
Temperature and humidity control
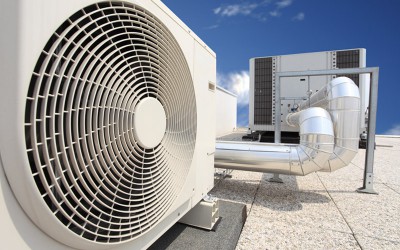
Air conditioning and heating
Ask a quotation or contact us
Those who have already chosen us...
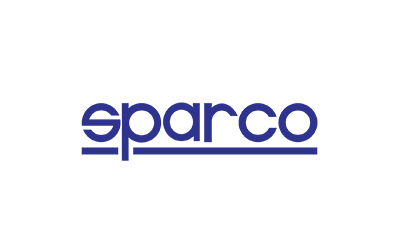
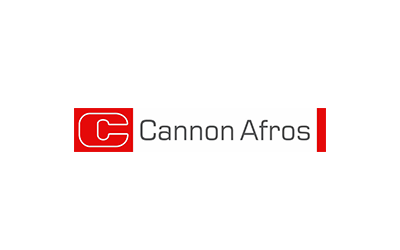
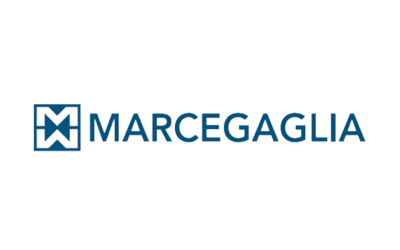
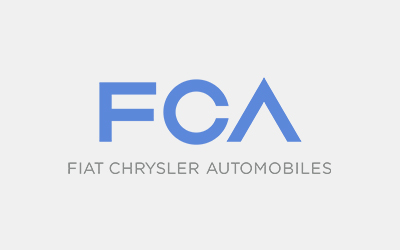
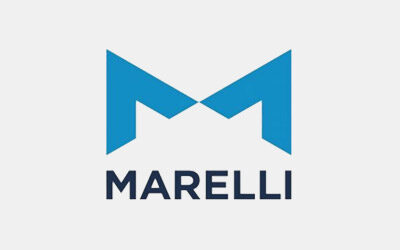

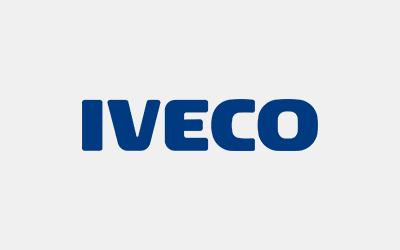
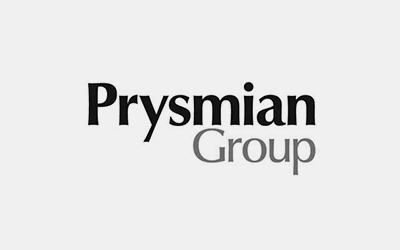
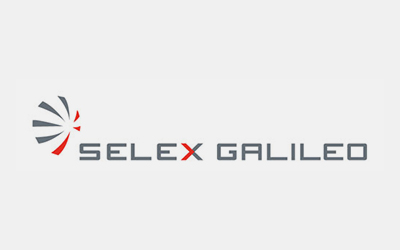
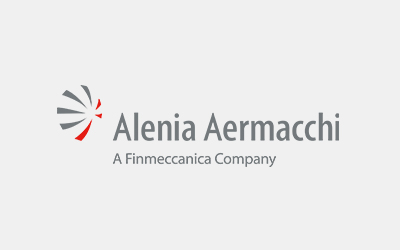
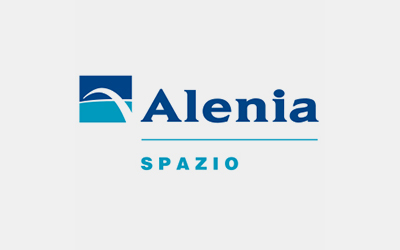
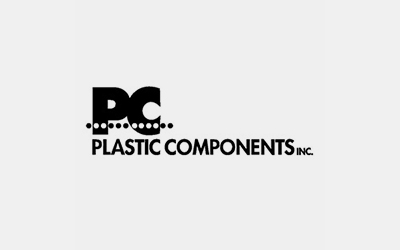
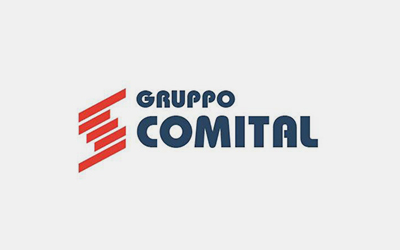
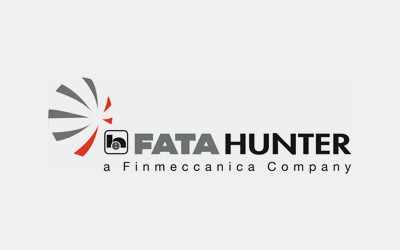
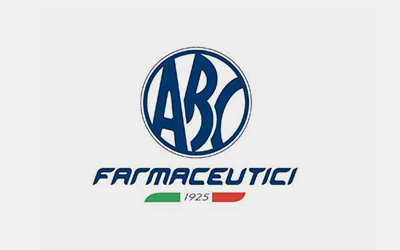
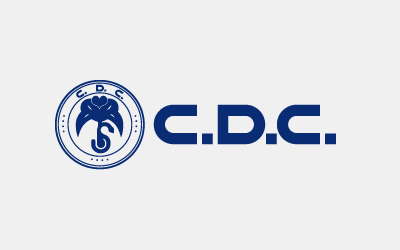